
Different Methods for Loop Tuning in Robotics

If all the input parameters are working fine and the system is not showing any dangerous output characteristics. If the system response of your system does not show any error and there is no need to improve upon its characteristics, you do not need PID. If your reference output and system output match, you get what you want, there is no need for loop tuning of PID. You do not need a PID controller under the following conditions: If the graph is linear, you can change parameter gains as a whole. For non-linear devices, characteristics properties and parameter values will change with change in the curve of the graph, which means at every point of the curve, you will need to change your parameter gains. You surely need a PID controller when your system is linear. There are certain conditions that decide if you need PID loop tuning or not. However not every robotic device will require you to put a PID controller and vary your parameters. PID controllers go hand in hand with robotics as they bring accuracy into the system. Robotics means automated control of machines.
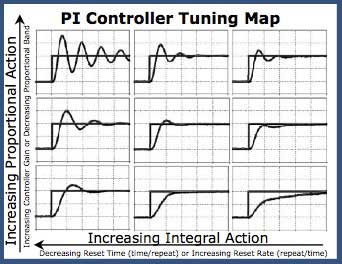
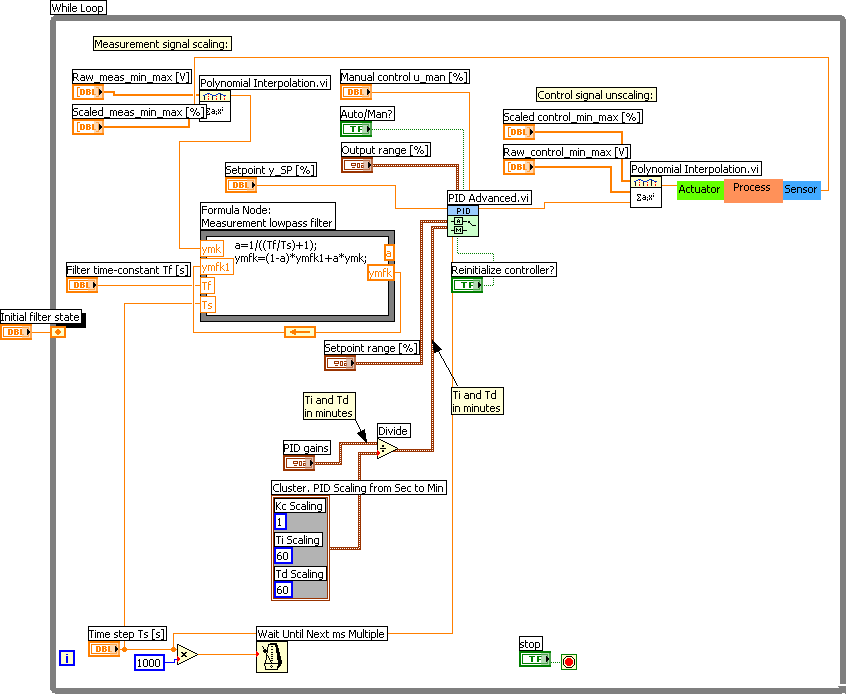
You do not need to vary all the three coefficients, you can change just one coefficient, or change two different coefficient by making combination or change all of them, depending upon your requirements and this is what we call loop tuning of a PID controller. The best thing about a PID controller is that it is tunable and scalable. A reference value is a standardized result and based on that, system output is changed to achieve desired results. A PID algorithm compares the system output against a calibrated or reference value. The PID, as the name itself implies has three main coefficients which affect the system response, varying these coefficients will give different results.
